What is Concrete | 20 Types of Concrete for Building Construction Industries
Introduction of Concrete:
The most widely utilised man-made material on the planet is concrete. It is a key building material that is utilised extensively in the construction of buildings, bridges, highways, and dams. It has a wide range of applications, including paviours, kerbs, pipes, and sewers.
Concrete is a composite material that primarily consists of Portland cement, water, and aggregate (gravel, sand or rock). When these ingredients are combined, a workable paste forms, which progressively hardens over time.
Concrete is available in a variety of forms, including:
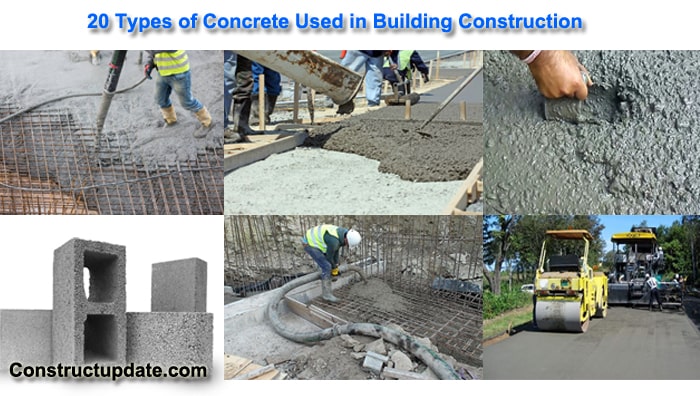
1. Reinforced Concrete
In industry and modern buildings, this type of concrete is commonly used. Place wires, steel rods, or cables in reinforced concrete before it hardens to increase its strength. Rebar is a more common term for these materials. Fibers have recently been employed to strengthen this concrete.
Tensile forces are resisted by these reinforcements, while compressive forces are resisted by the concrete itself. They form a strong bond, allowing the two materials to withstand a variety of applied stresses.
2. Normal Strength Concrete
The 1:2:4 ratio is used to blend all of the fundamental materials — concrete, sand, and aggregate. As a result, normal-strength concrete is produced. It takes 30 to 90 minutes for the concrete to set, depending on the weather conditions at the concrete site and the qualities of the cement.
It’s typically utilised for pavements and structures that don’t require a lot of tensile strength. It’s not suitable for many other constructions because it can’t sustain the strains caused by wind and vibrations.
3. Prestressed Concrete
Prestressed concrete units are used in many large concrete projects. Prestressed concrete is made utilising a unique method. It has bars or tendons, just as reinforced concrete. However, before the concrete is applied, these bars or tendons are stressed.
These bars are positioned at either end of the structural unit where they are employed when the concrete is mixed and installed. This unit is compressed after the concrete has hardened.
4. Plain or Ordinary Concrete
With its components of cement, sand, and aggregates, this concrete follows the conventional 1:2:4 mix pattern. It can be used to produce pavement or buildings that do not require a lot of tensile strength. It confronts the same problems as regular concrete in that it is susceptible to vibrations and wind stress. Dams can also be built with plain or common concrete. The long-term durability of this type of concrete is excellent.
5. Precast Concrete
Precast concrete is manufactured and cast in a factory to exacting standards. The precast concrete units are subsequently delivered to the job site and put together.
As you drive down the highway, you’ll see these units being carried to job sites all the time.
Precast concrete is used for:
- Concrete blocks
- Precast walls
- Staircase units
- Poles
The advantage of using precast concrete is how quickly it can be put together. The units are of very good quality because they are created in a factory.
6. Lightweight Concrete
Any concrete with a density of less than 1920kg/m3 is considered lightweight. Lightweight aggregates are used to make lightweight concrete. Aggregates are components that increase the density of a concrete style. Natural materials like scoria or pumice, manmade materials like clays and expanded shales, and processed minerals like vermiculite and perlite are all examples of lightweight aggregates. The fact that it has a very low thermal conductivity is its most important feature.
Lightweight concrete is commonly used to construct long-span bridge decks and construction components. Steel constructions can also be protected with it.
7. Air-Entrained Concrete
Every cubic foot of certain concrete contains billions of small air cells. The internal pressure on the concrete is relieved by these tiny air pockets. They have microscopic chambers that allow water to expand as it freezes.
Various foaming agents, such as alcohols, resins, or fatty acids, are used to entice air into the concrete during the mixing process.
8. Volumetric Concrete
To solve the problem of great distances between the concrete plant and construction sites, this concrete was developed as an alternative to ready-mix concrete. It necessitates the use of volumetric mobile mixers, which are specialized trucks. They transport the concrete materials as well as the water that will be mixed on the job site.
9. Decorative Concrete
Concrete mixtures with decorative concrete are visually and aesthetically pleasing. Decorative concrete can be made in a variety of ways, such as:
- Coloring
- Molding
- Polishing
- Etching
- Applying decorative toppings
10. Ready-Mix Concrete
Ready-mix concrete is concrete that has been prepared and soaked at a centrally located factory. This concrete is mixed on the way to the job site in the famous cement trucks that can be seen on city streets and highways. Because the cement does not require further treatment once it arrives at the jobsite, it may be used right away. Ready-mix concrete is a type of specialty concrete that is made according to precise requirements.
Ready-mix concrete is favoured over on-site concrete because the composition is more precise, and having the concrete ready to pour reduces workplace confusion. Buildings, roadways, walls, and other structures can all benefit from ready-mix concrete.
11. High-Density Concrete
The use of high-density concrete is quite particular. It’s extensively used in nuclear power plant building. The use of heavyweight aggregates in the production of high-density concrete aids the structure’s radiation resistance.
12. Rapid-Set Concrete
You’ll need rapid-set concrete if you’re in a hurry. It’s perfect for when you don’t have a lot of time to finish a project. It has a faster set time and is resistant to low temperatures, making it suitable for use throughout the year. It’s especially beneficial in the winter, when the cold prevents the usage of many other types of concrete.
13. Smart Concrete
This is the future’s concrete technology. It provides a new technique to keep track of the state of reinforced concrete structures. A standard concrete mixer is used to add short carbon fibres to the concrete. When the concrete is under strain or stress, this has an impact on its electrical resistance. This type of concrete can be utilised to discover potential issues before the concrete fails.
It excels at detecting minor structural defects.
14. Pumped Concrete
If you’ve ever pondered what type of cement combinations are used in the flooring of a really tall structure, you’ve definitely come across pumped concrete. Pumped concrete’s secret is that it’s very workable, allowing it to be quickly transported to a higher floor via a conduit. The concrete will be discharged through this conduit, which will be a flexible or stiff hose.
Pumped concrete can also be used:
In order to make superflat floors on lower structures,
Roadways and bridges are examples of construction projects.
Swimming pools, for example, are more personal goods.
15. Limecrete
Instead of cement, this concrete is made with lime and lightweight particles like glass fibre or sharp sand. It is mostly used to construct floors, vaults, and domes. Limecrete has numerous environmental advantages due to its ease of cleaning and renewable nature. It’s also suitable for radiant floor heating.
16. Roll Compacted Concrete
A big roller compacting a layer of concrete is a common sight on many American freeways. Roll-compacted concrete is a strong, dense concrete that is utilised on highways with heavy traffic and cars carrying significant loads.
17. Pervious Concrete
One of the most frequent types of concrete used in the construction of roads and pavements. It was created to address the issues of stormwater runoff, puddles, and pools of water on highways and airport runways.
Water is absorbed by other types of concrete. Pervious concrete roads offer fewer issues with hydroplaning, tyre spray, and snow buildup. It also reduces the requirement for storm sewers and curbs.
18. Glass Concrete
Glass concrete is a more modern type of concrete that incorporates recycled glass. When aesthetic appeal is a key factor in the concrete’s design, this type of concrete is used.
19. Asphalt Concrete
This type of concrete, often known as “asphalt” or “blacktop,” is commonly used on roads, airport runways, highways, parking lots, and sidewalks – practically anyplace pavement is required. Asphalt is a dark material made up of a hydrocarbon combination known as bitumens.
20. Shotcrete Concrete
Shotcrete is distinguished from other types of concrete chiefly by the method of application. Shotcrete is sprayed onto a frame or formwork using a nozzle. Because this application necessitates a higher air pressure, the compaction process occurs concurrently with the placement.
Shotcrete can be used to repair wood, concrete, or steel constructions that have been damaged.