Concrete Pumpability Factors | Pumpable Concrete Factors Affecting
Pumpable concrete is a type of concrete that can be transported to a great height via pipes and is utilised when a large amount of concrete needs to be laid.
Several factors affect the pumpability of concrete, including cementitious materials, aggregate properties, admixtures, and batching and mixing of concrete ingredients.
Various cementitious ingredients, such as fly ash and silica fumes, improve the performance of pumped concrete. As a result, the maximum aggregate size should not exceed one-quarter of the diameter of the pumping pipe, and caution should be exercised while mixing lightweight and heavy-weight aggregates in concrete.
Furthermore, batching and mixing must be done correctly and thoroughly; otherwise, concrete pumping complications may emerge.
What are the Factors Affecting Concrete Pumpability?
I. Cementitious Materials
In general, pumped concrete bleeding is a big issue that must be avoided, and fine cement is utilised to solve the problem. As a result, finer cement is preferable.
Since of its spherical particles and glassy texture (see Figure-3), fly ash is an excellent choice for pumped concrete because it improves the mixture’s cohesiveness and reduces the amount of water required.
Another additive that can be used to improve the pumpability of concrete is silica fume. Furthermore, it considerably improves the concrete mixture’s cohesiveness.
Furthermore, because the shape and texture of its particles are similar to that of Portland cement, ground granulated blast furnace slag may marginally increase the pumpability of concrete.
Concrete segregation is more possible if a considerable percentage of ground granulated blast furnace slag is included in a combination containing heavyweight material. Furthermore, the use of ground granulated blast furnace slag delays concrete setting time, which can be beneficial in some cases.
II. Concrete Aggregate Characteristics
a) Concrete Aggregate Size
The maximum aggregate size used to make pumpable concrete should usually not exceed the minimum pumping pipe diameter divided by four.
This is because if the maximum aggregate size surpasses a quarter of the minimum pipe diameter, the risk of segregation increases.
As a result, careful selection of aggregate size is essential to achieve the desired cohesiveness in a concrete mixture.
There are aggregate blending standards that can be quite helpful in terms of optimising ingredients and generating well-graded aggregate. Finally, after the aggregate grading has been set, it is critical to preserve uniformity.
b) Concrete Aggregate Shape
Most aggregate shapes are suitable for pumpable concrete as long as the void ratio is kept to a minimum. Because round gravels do not create friction internally or with the pipe system, it is preferable to utilise round-shaped aggregate for pumpable concrete. As a result, they can readily pass through pipes, particularly in corners and tapering areas of a pumping system.
Because the void ratio of angular aggregates can be reduced and, eventually, pumpable concrete can be formed, they should not be completely discarded.
c) Concrete Aggregate Density
If the density of different particle sizes in a concrete mixture differs, bleeding and segregation of pumped concrete will be exacerbated. Furthermore, if lightweight concrete is made incorrectly, the lightweight aggregate may float out, causing problems during concrete laying.
Under pumping pressure, lightweight aggregate absorbs a substantial amount of water in the concrete. Pipeline obstruction will occur at some point. Furthermore, when the pump pressure is removed, the absorbed water leaks out of the aggregate, causing bleeding, especially during the installation of concrete slabs.
III) Admixtures
Admixtures are commonly employed in most applications, and they have a significant impact on concrete pumpability. Water-reducing admixtures and high-range water-reducing admixtures, for example, are helpful because they reduce free water content and prevent the use of unnecessary cement content.
The addition of an air-entraining additive to concrete increases the mixture’s cohesiveness and pumpability. Providing an air-entraining agent, however, has little benefit if the cement concentration of the mixture is high.
IV) Material Batching and Mixing
Problems in batching, the amount of mixing water used, and other probable errors that occur during material batching have a significant impact on pumpable concrete. As a result, precision in concrete batching is necessary.
Pumpable concrete should be adequately mixed, and machines used for this purpose should be utilised according to the manufacturer’s recommendations. Finally, before placing ready-mix concrete into the pump, it’s a good idea to mix it up.
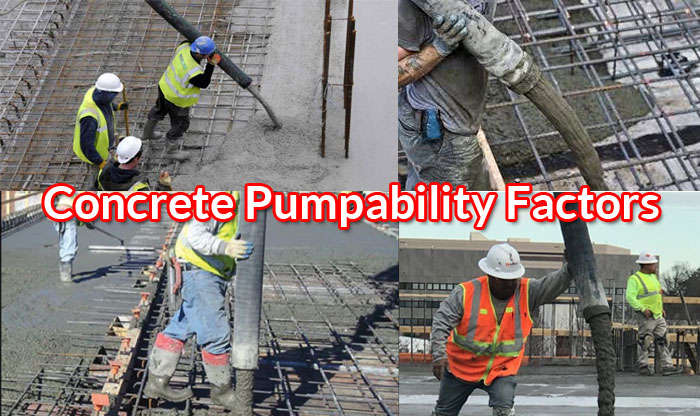