Ultra-High Performance Concrete (UHPC) Explained
What is Ultra-High Performance Concrete (UHPC)
Due to its extraordinary strength and endurance, Ultra High-Performance Concrete (UHPC) is a new kind of concrete that has been developed recently. This high-performance concrete has a variety of uses, including expedited bridge construction and structural restoration. Continue reading to discover more about UHPC.
With specified durability, tensile ductility, and toughness requirements, Ultra-High Performance Concrete (UHPC) is a cementitious concrete material with a minimum specified compressive strength of 17,000 pounds per square inch (120 MPa). Fibers are typically added to the mixture to achieve the specified requirements.
Reactive powder concrete is another name for Ultra-High Performance Concrete (UHPC) (RPC). Typically, Portland cement, other cementitious materials, reactive powders, limestone or quartz flour, fine sand, high-range water reducers, and water are used to make the material. The material can be designed to have compressive strengths more than 29,000 psi (200 MPa).
The thick, smooth surface produced by using fine materials for the matrix is prized for its aesthetics and capacity to accurately transmit form details to the hardened surface. Flexural strengths of at least 7,000 psi (48 MPa) can be attained when mixed with metal, synthetic, or organic fibers.
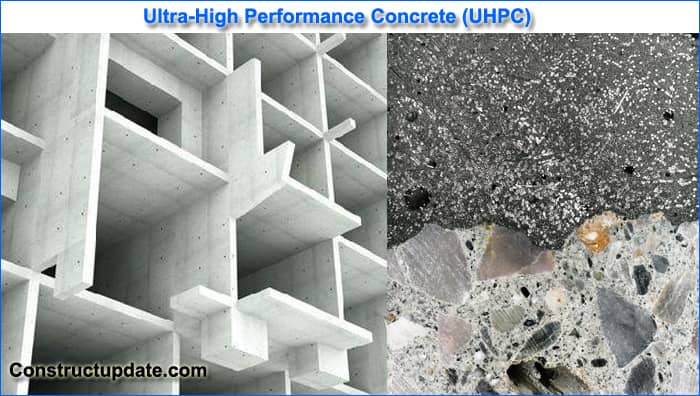
High carbon steel, PVA, glass, carbon, or a combination of these fibre types or others are frequently utilised in UHPC. The ability of this material to deform and support flexural and tensile stresses even after initial fracture represents a first for concrete.
In applications like closure pours between precast pieces, the high compressive and tensile capabilities of UHPC also provide a high bond strength, allowing for shorter embedment lengths of rebar.
Due to its excellent flow properties and ability to self-compact, UHPC construction is made simpler in applications where the use of reinforcing steel is not necessary. The UHPC matrix exhibits low permeability (less than 0.02 x 10-12 m2/s for chloride ion transport) due to its high density and sparse interconnected pore structure. It offers remarkable durability qualities since harmful elements like chlorides can’t enter the material due to its low permeability.
A few producers have developed pre-mixed UHPC formulations that only require the addition of water. American Society for Testing and Materials (ASTM) has developed ASTM C1856/1856M Standard Practice for Fabricating and Testing Specimens of Ultra-High-Performance Concrete, which is based on current ASTM test procedures but has been modified to be appropriate for UHPC. An illustration of the variety of material properties for UHPC is as follows:
Strength
- Compressive: 17,000 to 22,000 psi, (120 to 150 MPa)
- Flexural: 2200 to 3600 psi, (15 to 25 MPa)
- Modulus of Elasticity: 6500 to 7300 ksi, (45 to 50 GPa)
Durability
- Freeze/thaw (after 300 cycles): 100%
- Salt-scaling (loss of residue): < 0.013 lb/ft3, (< 60 g/m2)
- Abrasion (relative volume loss index): 1.7
- Oxygen permeability: < 10-19 ft2, (<10-20 m2)
Strategies for UHPC Production
By removing the coarse material from the mixture, you can increase the homogeneity of concrete.
Improve the density of the concrete by optimising the gradation and mixture proportions between the main components of the mixture. This is done by reducing the space between mix component particles.
To make the concrete more ductile, steel fibres can be added to the concrete mixture. Steel fibres must be added to the mixture at a minimum of 2% by volume to help prevent concrete from becoming brittle. Variables such as the fibre aspect ratio, shape, and UHPC production issues including workability control the maximum fibre content.