What is Concrete | Cement Properties | Types of Concrete
What is Concrete?
Concrete is a composite material made by mixing binding materials (cement or lime) with aggregates (sand, gravel, stone, brick chips, etc.), water, admixtures, and other ingredients in precise proportions. The mixing proportions determine the strength and quality of the product.
Concrete is a very important and valuable building material. The cement and water begin a reaction with one another to bond themselves into a hardened mass once all of the constituents – cement, aggregate, and water unit of measurement – are mixed in the proper amounts. This causes the concrete to harden into a rock-like mass.
Concrete is the bone of building construction. There are many types of concrete used in building construction work.
Types of Concrete
Regular Concrete
Regular concrete, often known as conventional weight concrete or traditional strength concrete, is the most common variety utilized. This refers to concrete that is immediately available for personal and domestic use in the retailer’s market.
This includes any usage instructions printed on the product’s packaging. Sand and other materials are used as aggregates, which are then consolidated in temporary vessels.
Roller Compacted Concrete
These are slabs of concrete that have been poured and compacted using earth-moving equipment such as big rollers. This concrete is mostly used for excavation and filling purposes.
These concretes have a lower cement concentration and are filled to your specifications. This concrete has a high density after compaction and cures into a solid monolithic block.
Lime Concrete
Lime is used as a binding agent in lime concrete. Unless otherwise specified, lime is normally blended with surki and khoa or stones in a 1:2:5 ratio. Before combining, the khoa or stones are soaked in water. The most common applications for lime concrete are foundations and terrace roofing.
Cement Concrete
Cement concrete composites are used as the primary building material in most engineering projects. Cement, sand, brick chips, or stone chips of the appropriate size make up the mixture. The common ratio is 1:2:4 or 1:3:6. For optimal strength construction, the concrete mix is cured with water for 28 days after mixing the needed amounts of components.
Ready Mix Concrete (RMC)
Ready-mix concrete (RMC) is a type of concrete that is made in a batch plant using a predetermined mix design. There are two common methods for delivering ready-mix concrete.
The barrel truck, sometimes known as in-transit mixers, is the first. This type of truck transports plastic concrete to the job site.
The volumetric concrete mixer comes in second. This method delivers a dry ready mix and then mixes the concrete on site.
Dry Ready Mix Concrete
During the preparation and bagging stages of dry mix concrete, no water or liquid is introduced, as the name implies. To manufacture the dry concrete mortar, thoroughly and uniformly mix the cement, sand, and aggregate until a consistent texture is achieved. This concrete can be stored in bags or in bulk for mixing with water on the job site. Bags can be delivered by vehicle or by a concrete transit mixer in big quantities.
Asphalt Concrete
Asphalt concrete, also known as just asphalt, is a composite material used to build roads, highways, airports, parking lots, and other types of pavements.
Asphalt was first used for street construction in the late 1800s, and as the motor industry increased, so did the market for asphalt.
Since then, the development of asphalt technology has progressed tremendously. Asphalt pavements are now built with highly complex equipment and techniques.
Transit Mix Concrete
All of the basic materials for transit mix concrete are placed straight into the truck mixer. There is no need for a plant mixer. At the plant, some or all of the mixing water is normally introduced. During loading, the mixer drum rotates at charging speed.
Ferro Cement Concrete
Fiber concrete should not be confused with Ferro cement concrete. Ferro cement is made up of tightly spaced wire meshes that have been soaked with a rich cement mortar mix.
Steel wires with a diameter of 0.5 to 1.0 mm are usually formed into meshes. Mortar is poured to the form-work with fabricated steel utilizing layers of wire mesh at a ratio of 1:2 to 1:3 and a water-cement ratio of 0.4 to 0.45.
The concrete will have a steel content of 300 to 500 kg/m3 of mortar. Due to the high amount of steel in the material, it has high ductility and tensile strength.
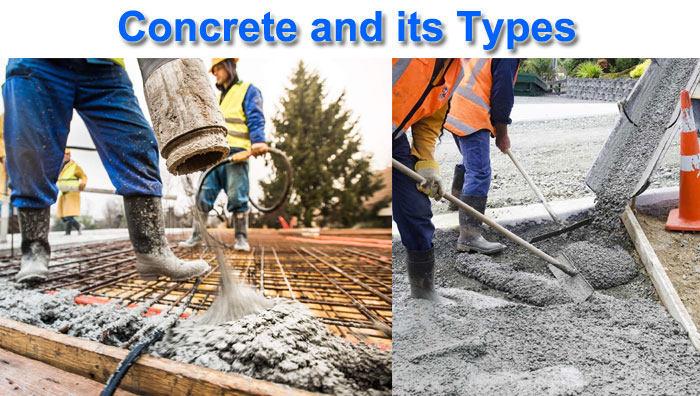